The Life-Critical Cold Chain
Vaccines, pharmaceuticals and many foods must be kept at specific temperatures while in transit or risk harming consumers. So how are carriers assuring temperatures—and safety?
The costs of cold-chain instability can be enormous—in both dollars and human lives. “We depend on cold chain and carefully forecast our need for vaccines as much as possible,” says Paul Molinaro, senior manager of Change & Development at UNICEF Supply Division. “Losing vaccines to spoilage or any other supply-chain factor is something we just can’t afford, since vaccines are life-critical and also very long to manufacture if they are lost.”
When refrigeration is inadequate, perishables like medicine and food can spoil and their quality alter by chemical reactions that begin to take place. This makes it essential to monitor the “cold chain”— the origin-to-destination distribution network of refrigerated products in temperature-controlled containers (reefers), trucks and warehouses.
“The vaccine cold chain is needed from the time a vaccine leaves a manufacturer to the point of delivery at the health center or immunization point,” says Andrea Sioris, a manager at UNICEF. “The cold chain is monitored through various mechanisms, such as vaccine vial monitors that check exposure to heat, as well as electronic time temperature monitoring devices, which track temperatures during international transport.”
“Countries return Vaccine Arrival Reports to UNICEF, in which the status of vaccines—including any temperature exposure—is recorded,” says Sioris.
Richard Smith, director of Life Sciences and Special Services at FedEx Express, says the life sciences and healthcare industries also have stringent demands for refrigeration. Pharmaceuticals must often be kept at temperatures between 15-55 degrees Celsius. “In other cases, a broader 10-30 degree Celsius range is acceptable,” he says. Biotech products and drugs on clinical trials both frequently require refrigeration between 2 and 8 degrees Celsius—significantly below the ranges of standard product refrigeration.
“We see high demand for cold-chain services in produce, flowers, fresh fish and other perishable goods,” says Smith. “During transit, time-sensitive and highly perishable goods like fish must be maintained at refrigerated temperatures to ensure freshness and prevent spoilage.”
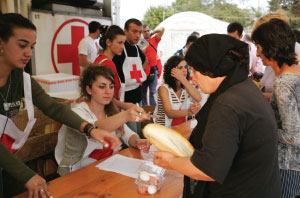
To answer the challenge, container atmospheric controls today go well beyond maintaining temperature. Fruits and vegetables respire as they mature, consuming oxygen and producing carbon dioxide and a hormone called ethylene. Kartik Kumar, director of Marketing and Strategic Planning, Global Container Refrigeration at Carrier Transicold, says his company “uses technologies that enable shippers to control levels of these gases in ways that can further slow the ripening process and help extend shipping time.”
While controlling humidity levels inside containers is important for flower bulbs, paper products, artwork, electronics and certain metals, health is concerned for pharmaceuticals and food items such as garlic, onions, ginger and other root crops. “The food we prepare comes from a variety of vendors,” says Melanie Pipkin, a Red Cross spokeswoman. “As food is checked in, we note the condition in which it arrives. Any food that doesn’t arrive in its acceptable temperature range is rejected.”
Shipments must be monitored throughout the cold chain, and it may be necessary to intervene when there is a failure. Some organizations place data loggers in the boxes of goods they are shipping to monitor for temperature control. Unfortunately, these companies usually receive monitoring results after the fact, so they lack real-time visibility.
“Without real-time visibility, shipments can spoil,” says FedEx’s Smith. “A shipping delay can be as simple as a transportation connection that is missed when you’re trying to expedite the shipping of a temperature-controlled drug or a medical device needed in a surgery.”
Years ago, Smith says, FedEx had a finite number of locations that provided refrigeration, and in many cases refrigeration was done on an ad hoc basis. “We made a strategic decision to grow our healthcare business,” he says. “This encompassed providing temperature-control services such as cold storage, dry ice replenishment and even gel pack exchange. What we wanted to do was to increase our cold-chain infrastructure in order to better manage contingency situations involving time and temperature-sensitive products.”
Today, FedEx averages around 20 scans on each shipment through its end-to-end shipping and distribution network. With some very critical packages, it is even using active sensors the size of a smart phone, which are inserted into shipping boxes and containers. These sensors report on a shipment’s temperature, humidity and integrity via a light sensor in real time and issues alerts in the event of a temperature excursion or package breach. Sensors also report a shipment’s exact location, thanks to incorporation of GPS technology. “Our customers can access this tracking and performance information through a web-based user interface called SenseAware,” says Smith. “We also have a 24/7 monitoring service.”
Even with diligent monitoring, however, failures still occur. “A lost or thawed sample means the patient has to give more blood. This can often mean another three-plus hour drive to get back to the nearest clinic or hospital,” says Mitch Nelles, vice president of Research and Development and Technical Operations for XDx, a molecular diagnostics company.
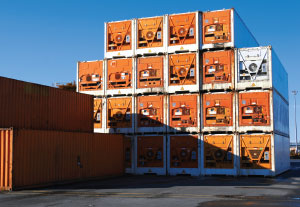
To improve outcomes, more companies are using electronic data recorders to monitor shipments. “The control systems are compatible with shipboard telemetry systems shippers use to monitor all refrigeration systems onboard,” Kumar says. “Some shipping lines are further engaging telemetry to relay seaborne refrigerated container status via satellite to land-based central monitoring points. But when a failure occurs, shipping lines carry ‘ship kits,’ which include key components for repairing a refrigeration unit at sea.” Carrier Transicold, he says, offers a comprehensive repair and service network with nearly 430 service centers worldwide in all major and developing ports.
FedEx also has a network of local hubs and gateways that protect temperatures of goods. “We look at the entire cold-chain backbone when we address refrigeration,” says Smith. “This means that there are numerous transit points en route to the 220 countries and territories around the globe that we serve which need refrigeration and backup controls and solutions. All of these hubs and stations are catalogued for their temperature-control capabilities and any one of them might be called into service if there is a system failover need generated by a shipment delay due to weather, regulatory hold or other factors.”
Rich Horan, vice president of Support Operations for medFusion, says cold-chain improvement efforts are paying off for his company, which provides clinical trials of new medications and uses sensors in its cold-chain management. “We have never lost a specimen,” he says, “and will continue to improve the process to minimize the potential for future failures from occurring.”
Cold Shipping vs. Global Warming
Shippers want sustainability and economy. Kartik Kumar, director of Marketing and Strategic Planning, Global Container Refrigeration at Carrier Transicold, says that costs of refrigeration vary depending on the number of refrigeration units carried on a ship and the amount and type of commodities within each unit. “The cost of fuel to generate electricity to run refrigeration units, as well as the emissions related to energy production can be significant, especially as fuel prices rise and energy becomes a greater contributor to the total cost of ownership (TCO) of a container refrigeration unit,” Kumar says. “Only 10 years ago, energy’s share of TCO was 28 percent and acquisition cost was the largest part, at around 57 percent (the balance being maintenance and repair costs). Today’s fuel prices put energy costs at about two-thirds of the TCO. Therefore, an upfront investment in fuel-efficient refrigeration units can save significantly over the life of a unit.”
Kumar notes that Carrier Transicold is currently in sea trials on an energy-efficient refrigeration system. The unit enhances its environmental profile by using carbon dioxide—a natural refrigerant with a global warming potential (GWP) of 1—rather than a synthetic refrigerant with a much higher GWP. “We have ushered in a new level of energy efficiency in containers,” says Kumar. “In one case, a shipping line with 6,000 of these energy-efficient containers is projected to eliminate more than 208,000 tons of carbon emissions.”
Best Practices for the Cold Chain
Technology advances will continue to change the cold chain. Shippers can capitalize on these advances by:
• Gaining end-to-end visibility of the cold chain
This starts with verifying the capabilities of your cold-chain service providers. You should strive for no “custodial breaks” in your cold chain—from the time you ship goods until they arrive at their final destinations. To achieve this, you need systems that monitor environmental controls every step of the way.
• Minimizing “handoffs”
The more you can work end-to-end with fewer service providers, the less coordination you will have to do between parties—and the less complexity.
• Improving internal cost management
Shippers tend to focus on containment of external costs, but there are also internal opportunities. “Traditionally, shippers endure heavy schedules on Monday, Tuesday and Wednesday, because they want to ship their temperature-sensitive goods so these goods aren’t stored in a warehouse over a weekend,” says Kinei Lin, manager, Customer Engineering at FedEx Express. “But with refrigerated trucks and distributed warehouse hubs with cold storage, we can pick up shipments on a Thursday or Friday. This flexibility helps to normalize the work week for shippers, because they can now spread their workload over the full five days and have their packages delivered earlier.”
Leave a Reply